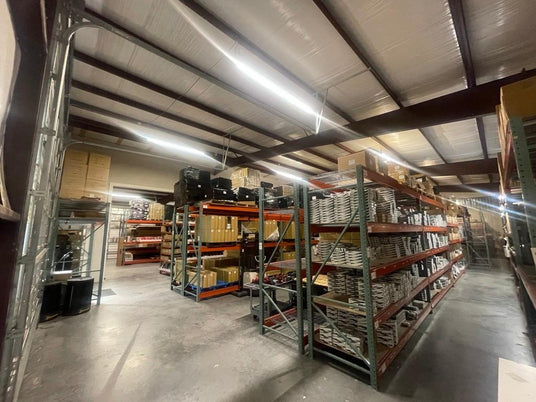
Storage Solutions
In the past, we tried various 3PL services but encountered significant issues: lost products, 3PLs that didn’t understand our parts, and the unique challenges posed by automotive aftermarket parts—ranging in size and weight from small detent springs to full welded bumpers, as well as slow-moving SKUs. It was difficult to find a 3PL that understood the automotive industry, and when we did, we were considered too small of an account. Because of this pain point, we decided to offer our own solution to others. Our goal is to scale by pooling resources with more brands. We are not just a 3PL; we exclusively service automotive brands.
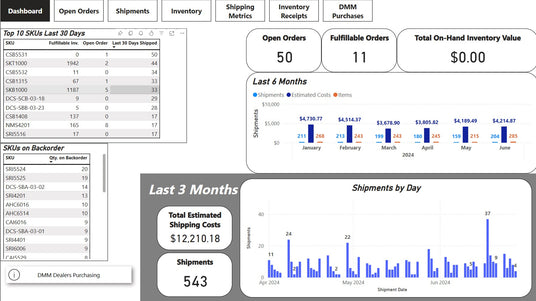
System Integrations & Data
We’ve built a dashboard system in collaboration with our in-house brands, focusing on the operational details that matter most to us collectively. This dashboard is a living system, regularly updated based on our brands' requests, ensuring it remains valuable and relevant.
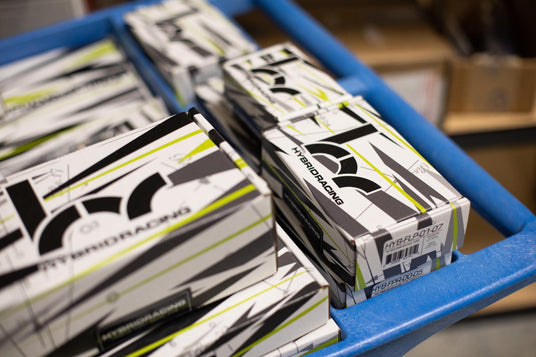
Order Fulfillment
In today’s world, Amazon has set the bar high. When it comes to shipping, consider it handled. Whether it’s a single package, a rock slider, or an entire pallet, our fulfillment process is built to meet those high standards. We ensure your products reach customers quickly and efficiently. We've got the experience and the systems to ship anything—from single packages to the heaviest pallets—because it's what we do every day.
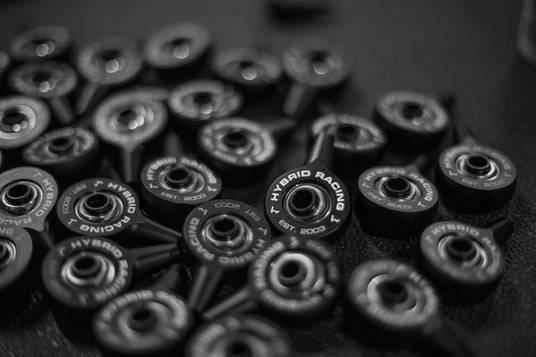
Kitting and Assembly
We know that some products need to be combined or assembled before they reach the customer. This began with our Hybrid Racing brand, where we assemble every shifter in-house, and has since expanded as we've realized the benefits of quality control and flexibility. Our brands often ask us to add special stickers, kit multiple sub-products together, and inspect dimensions. We collaborate with our brands to create detailed build guides and can set up automatic triggers based on your needs, such as build-to-order triggers. Our kitting and assembly services ensure that each product is perfectly prepared and presented, maintaining high standards of quality and consistency.
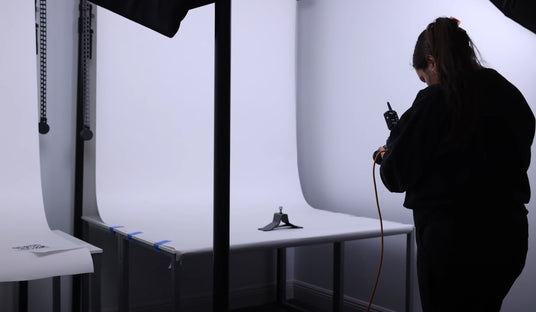
Product Photography
We take product photography seriously. Our photo room is equipped with tethered cameras to capture every detail, ensuring your product is shown accurately and clearly.
We also have a sound stage room for creating dynamic content. This space allows us to produce videos that highlight every angle and feature of your product.
For installed shots, we use our dedicated shop space to install and photograph your products in real-world scenarios. From under the hood to fully assembled setups, we show exactly how your products fit and perform.
Our aim is to provide clear, detailed visuals that help customers understand and appreciate your products.
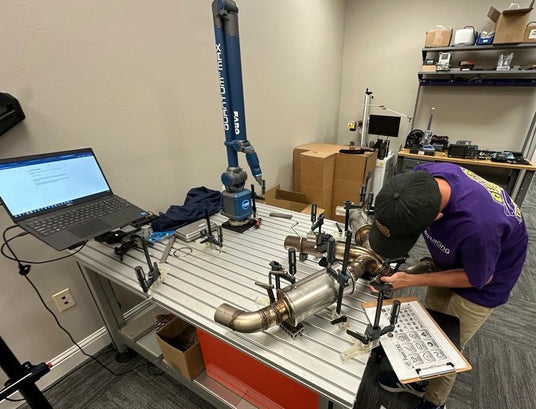
Inspection Services
We offer three levels of part inspection services. First, our trained assembly team handles the initial inspection, checking for scratches, color discrepancies, and general fitment issues. Second, our in-house mechanical engineers, who mainly develop parts for our brands, are available for advanced inspections using specialized tools like pin dowels or CMM inspection. Finally, we partner with Louisiana State University, leveraging their material science lab for comprehensive material inspections using machines like Instron tensile testers, hardness testers, Charpy impact testers, and more.